Share
Pin
Tweet
Send
Share
Send

To perform small work in the form of engraving and embossing, it is important to have a special tool, one of which is a small hammer. Its dimensions and low weight allow you to:
- perform small work without fear of damaging other elements;
- work for a long time without fatigue in the hands;
- optimally distribute the impact weight, controlling the applied forces.
The cost of such a tool can be quite high. Therefore, many masters prefer to make it themselves, while adjusting its parameters to fit your needs. They use the usual railway crutch for this.
The process of making a hammer from a railway crutch
We choose a railway crutch. It must be free of obvious defects or deformations.
We crutch the crutch in a vice, and completely remove rust deposits from it. For this we use a grinding machine.

And a belt grinding machine.


At this stage, it is very important to remove all traces of corrosion, even if they are deeply ingrained in the metal.

If we are going to make two hammers from one crutch, then we need to measure their length in advance by dividing our workpiece approximately in half.
In each half in the middle we outline a hole for the handle.

Using a drilling machine we make the necessary holes. The pen usually has an oval profile. Therefore, for each hammer, 2-3 holes will be located, located as close as possible to each other.
At the next stage, we use the file to process the resulting holes, connecting them until an oval profile is obtained. We also process the entire workpiece, removing all burrs.


Cut the workpiece into two parts, getting two types of hammers. One will have a standard look, and the second will get a wide heel.
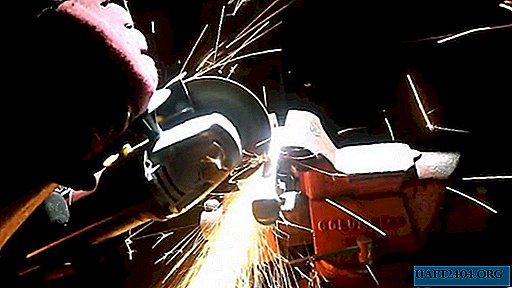
For the manufacture of tool handles we take solid wood. When choosing the length, we focus on our personal preferences and production need.
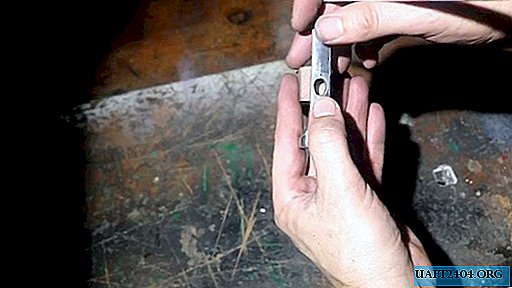

Handle blanks are treated with a special file, giving them the required shape.

Also create a footprint under the hammer. On the seat we make a cut for the installation of the wedge.

At the assembly stage, epoxy is bred, which covers the seat. Next, put a hammer on the handle and wedge it.

The rest of the handle on the other side of the hammer is removed, and the wooden product itself is coated with oil.


All these operations are carried out with the second hammer.
As a result, we got such beauty:





Share
Pin
Tweet
Send
Share
Send