Share
Pin
Tweet
Send
Share
Send
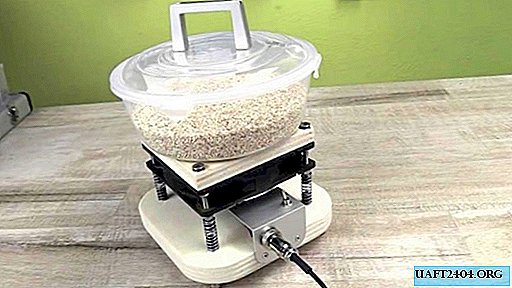
At first glance, it is not so easy to determine the purpose of this device. A transparent plastic cup with a handle; cereal is poured into it, but it does not seem to be going to be cooked: after all, plastic and spirals are not visible, and the cereal is not filled with water, although there is an electric cord. Maybe the product is wet and needs to be dried? And it doesn't look like that.
Well, and when, opening the lid, they put old coins faded from time to time, and turned on the device and it “danced”, then the perplexity instantly dissipated. The device is designed for vibrational cleaning of small metal objects!
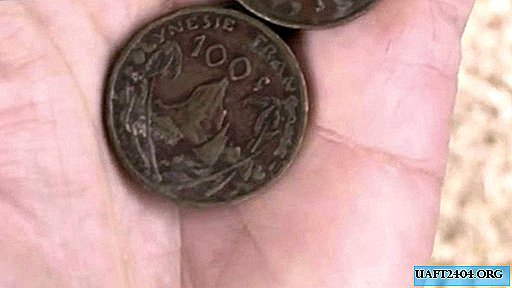
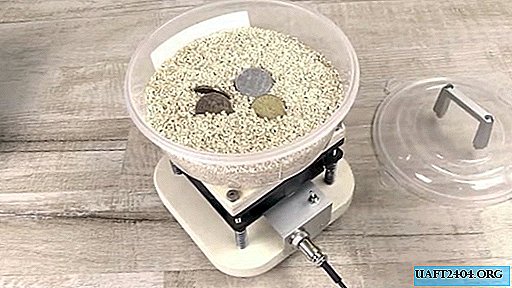
This assumption with brilliance (in the literal and figurative sense) was confirmed when the device was de-energized and stunningly clean and bright coins were extracted from under the croup (even the eyes became painful!), Which a few minutes ago made us melancholy and unattractive.
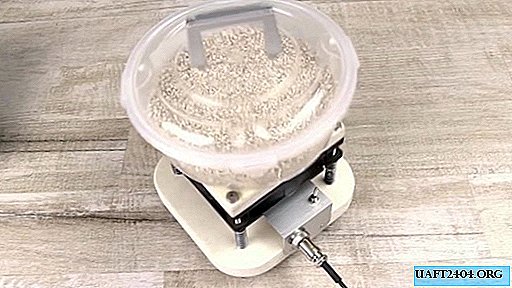
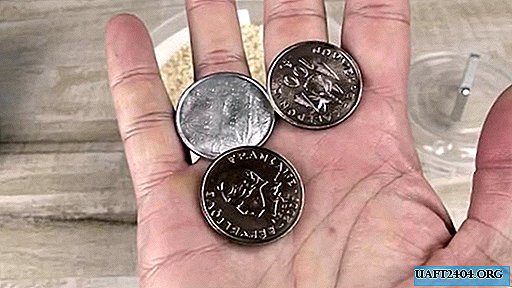
The same thing happened with steel bolts, nuts, brass or bronze bushings, and something else that obviously went in the past. There is plenty of dirt, soot and rust on them. However, placed, like the old coins, in the croup in which they had been staying for some time with the machine turned on, they did a miracle - everything became like new. Just unbelieveble!
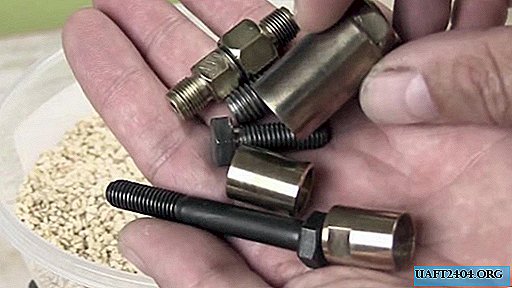
Is it possible to do something like this with your own hands? Easily! A special deficit is not required, so, all the little things and some kind of tool. But in order not to be distracted while working on a homemade product, we nevertheless denote the main thing that is needed.
Necessary tools and materials
From the tools you will need:
- Paint knife, scissors.
- Marker, ballpoint pen, ruler.
- Electric drill with a set of drills, electric jigsaw.
- Different wrenches, hand screwdriver, hexagon.
- Pliers, pliers, file.
- Soldering iron, soldering tools.
- Medical syringe.
Materials required for work:
- Household exhaust fan.
- Plastic round container with snap fastener.
- A piece of multilayer plywood and non-thick rubber
- Steel springs - 4 pcs.
- Screws with different heads and lengths with washers and nuts.
- Bolt with nut.
- Screws are short with wide heads and washers.
- Glue of the Motorsil brand.
- Electrical connector and on / off switch, etc.
The process of manufacturing vibration
Let's start with the compression springs. They should be sufficiently elastic with flat ends. It is the springs with unbalanced impeller that will provide the vibration process.
To fix the springs in the structure with screws, we insert rubber strips on both sides, which should form cylinders when folded (the ends of the strips should converge in place).



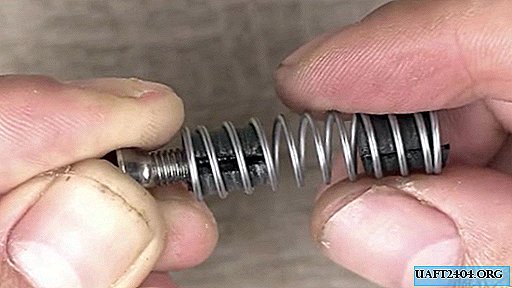
We proceed to the modernization of the computer fan, the impeller of which consists of 7 blades and is fully balanced. If you bring power to the device, it will work without vibration and beating.
To upset the balance, on one of the blades we drill a hole for the bolt and securely fasten it on the other side with a nut.


As a result, the weighted blade during rotation will create an imbalance and, if the fan is not kept on, it will make intricate “pirouettes” on the table surface.

Next, we cut the bottom base from multilayer plywood using an electric jigsaw. We drill holes in the four corners using the fan casing as a template. Then, using sufficiently long screws with washers and nuts, we securely fasten them together using wrenches and a hexagon.


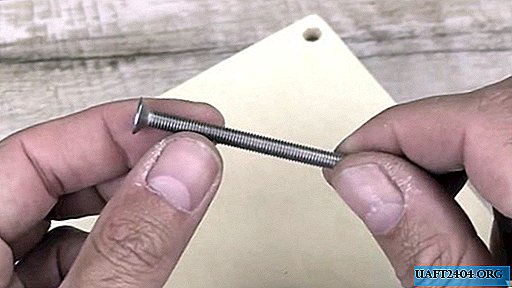
We are convinced that the system has not lost its imbalance. On the reverse side of the fan, we fix the protective net with washers and nuts, using the protruding ends of the screws, onto which we screw the springs with rubber inserts, which at the same time serve as nuts.

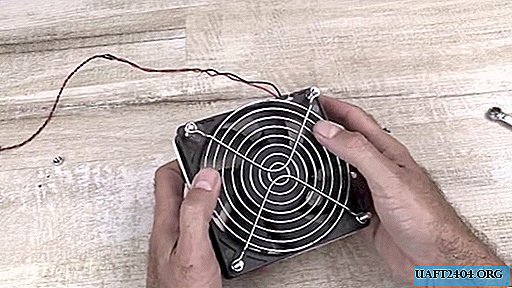
The presence of four springy "legs" at the corners in conjunction with the imbalance of the impeller provide a multidirectional and multi-frequency vibration process of the assembled structure.
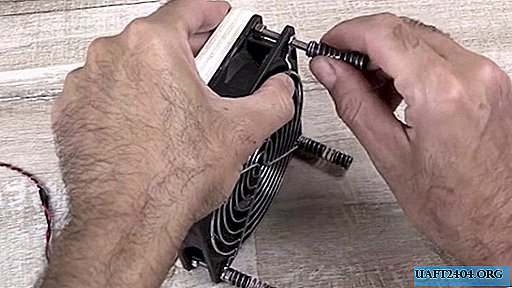
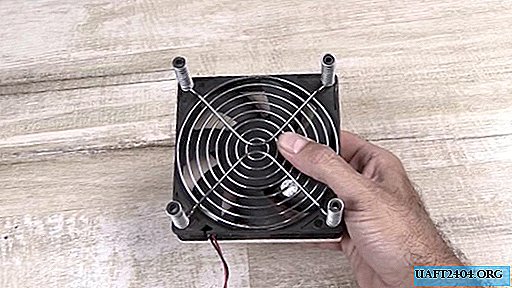
From the remaining piece of rubber, using a small bearing, ballpoint pen and scissors, we cut 4 circles, in the center of which we drill small holes. They will be needed to securely fix the plastic container to the upper base of the device along with four short screws and metal washers.
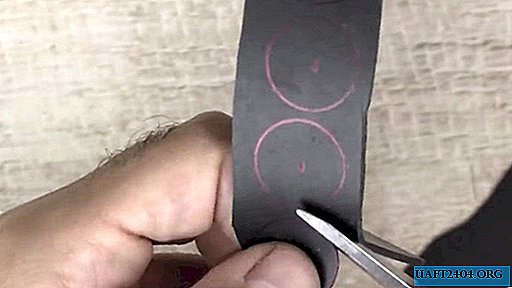

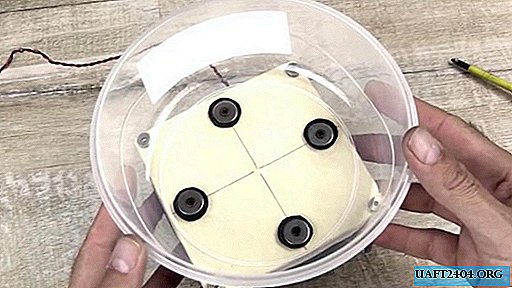
Next, we cut out the bottom base from the remaining piece of multilayer plywood, rounding the corners, and drilling 4 through holes in them, using the fan casing as a template. On the continuation of the diagonals drawn through the opposite holes, at equal distances from them, we make marks of the centers of the blind holes for one more "legs", but not spring ones anymore.

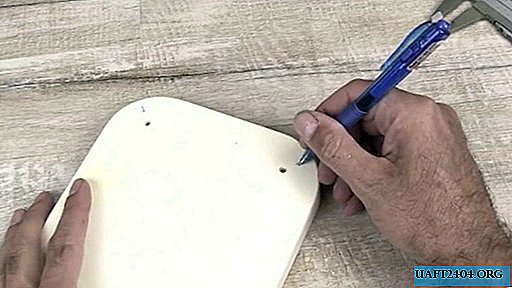
As supports, we use screws with round heads for a hexagon. So that they do not create additional resistance to the vibrational movements of the device, we fill their heads with glue of the brand Motorsil, which after hardening acquires not only strength properties, but also elastic ones. To obtain a spherical shape, we put on cambrices on the screw heads, into which glue is poured with a syringe.



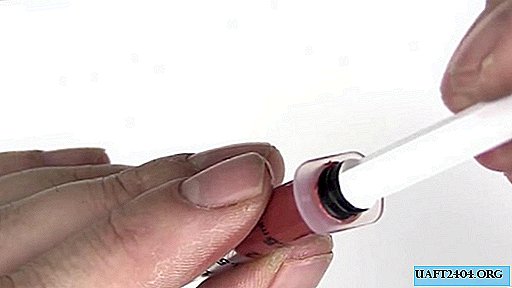



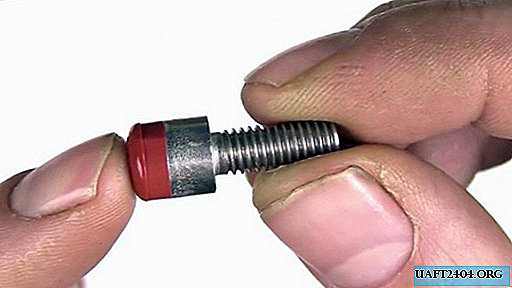
Screws modified in this way are screwed into blind holes that are drilled with a drill in previously marked places. For a tight and secure fit, tighten them with pliers.
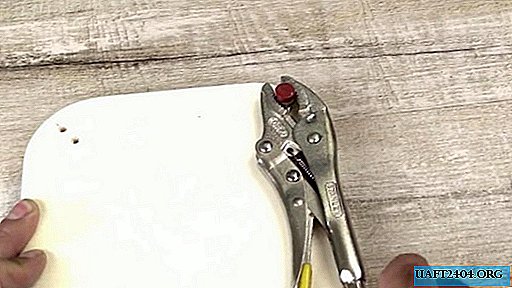
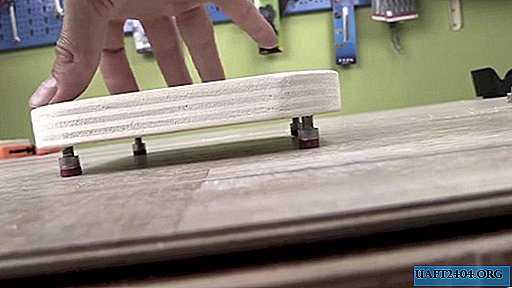
Now you can connect the lower base through the already existing holes with the spring legs of the upper platform by means of screws, screwing them into the rubber "nuts" in the springs.

We proceed to the installation of the electrical part. We need to install an electrical connector and a two-position switch. As a basis for them we use a duralumin corner. On one shelf, we drill a large hole under the connector and two small holes for mounting screws, on the other - under the switch. We round the upper corners along an arc of a circle using pliers and finish with a file.

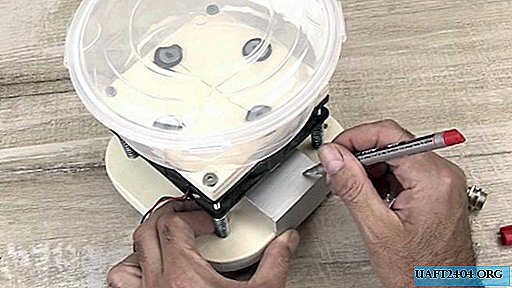

Now we estimate how long to leave the fan wires with a small margin, and cut off the excess with wire cutters. Pass one wire through the connector mounting nut and solder to one of its contacts. We solder a small piece of wire to its other contact, with which the connector will be connected to the switch. After some time, we push the cambrices to the soldering sites so that they slightly melt and tightly cover the contacts. It remains only a nut on the back of the shelf to fix the electrical connector in the space provided for it.
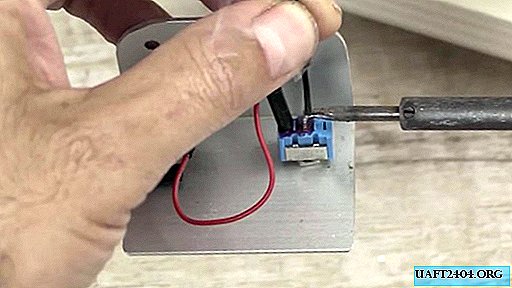

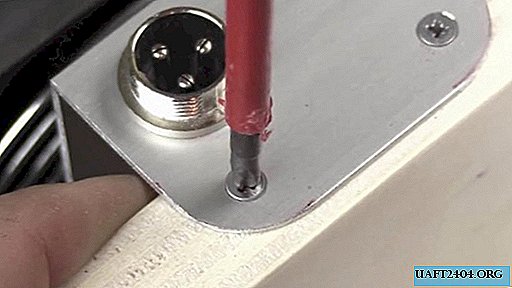
We do the same manipulations with the switch: we fix it on the shelf, solder the end of the short wire from the connector to one contact, and the second fan wire to the other. It remains only to attach the corner with the fastened elements with two screws to the end of the lower base.
In order to make it convenient to remove and install the cover, we fix the duralumin handle on it with the help of long screws passing through the through holes in the handle and the cover with washers and nuts.

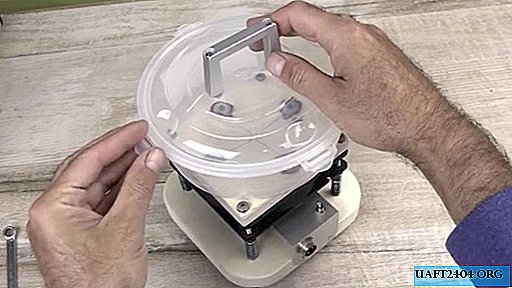
Now it’s enough to power the device and pour the cereal into the container, and it is ready to work. By the way, the noise created by our homemade product is 58-59 decibels, while the electric jigsaw gives out all 77-78 decibels.

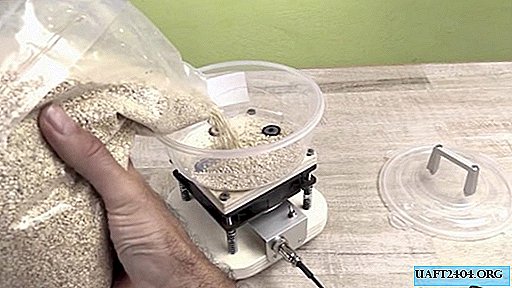
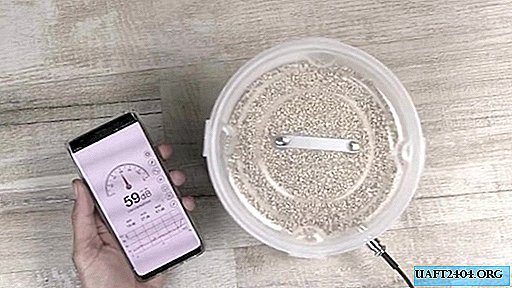
We test the vibration cleaner in practice, alternately loading old metal parts and used coins. The result is beyond praise. By the way, during vibration cleaning, the lower base is almost motionless (the bolt does not fall). This indicates a lack of energy loss.


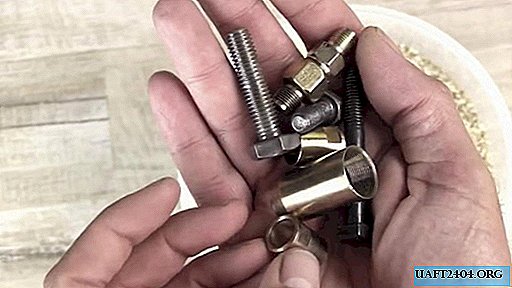
Improvements and improvements
The main problem is impeller imbalance. Its bearing and motor axis are not designed for this mode of operation and will quickly break. You can get out of the situation by using a drive with a displaced center.
The plastic container under the action of the load will first become dull, and after a while it will be wiped. Replacing with metal or glassware will extend the life of the product.
In the description, wheat grits were used as an abrasive load, but grains and other cereal crops can be used. To process the thread on the parts (in general, small elements), it is better to mix the cross section with the whole grain. For hard materials, crushed nutshells and even sand can be used.
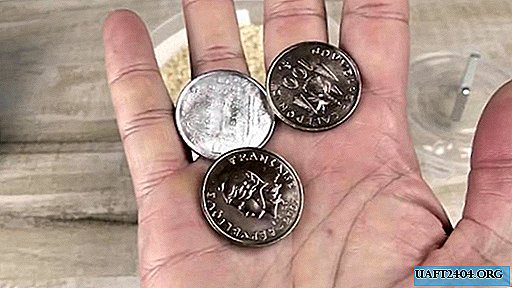
Share
Pin
Tweet
Send
Share
Send